PLATE DESIGN
The construction of the inlet part makes a perfect distribution of the liquids across the heating surface. The inlet part is
increased and supplied with channels preventing “dead spots” bacteria in the plate heat exchanger. The inlet with channels
secures a strong inlet part with a minimum of contact points.
The inlet parts are constructed with a leakage drained zone fulfilling the 3A specifications. The plate pattern is constructed to
obtain a high thermal efficiency. The pattern is available in two designs with different angle sizes giving high respectively low
turbulent flow. Combining these in a plate pack an optimal plate composition can be calculated. The angle and fishbone
pattern has appeared to make the best heat transmission by a given pressure drop.
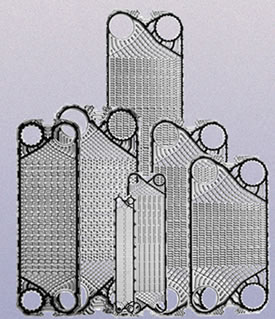
FREE FLOW PLATES |
Free Flow plates are designed for liquids containing fibers or other particles which
may clog up a traditional plate heat exchanger. Free Flow plates are designed without
metal contact between the plates in the liquid area giving a high turbulence and thus
a high heat transmission coefficient and especially a long power time.
Further advantages and Areas of Application
- The plate construction makes a strong and stable plate.
- To be applicate in the paper- and cellulose industry.
- To be applicate for cooling of mustard, tomato sauces and other viscous products.
- CIP-cleaning is possible.
- The construction of plates and gaskets according to 3A sanitary standards.
|
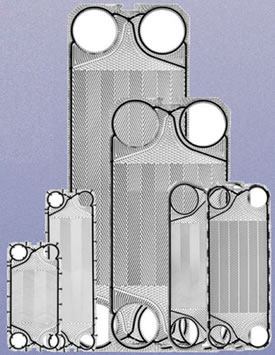
SEMI-WELDED PLATES |
Semi-welded plates are built up in plate cassettes. A plate cassette is 2 plates welded
together by means of laser welding. The advantage by this construction is on the one
side a welded plate channel and on the other side a traditional plate channel with
gaskets making assembling and cleaning of this side easier. On the welded side there
are two specially produced corner hole gaskets creating the tightening between the
two cassettes. Thus the gasket is reduced to a minimum on the welded side.
- This type of heat exchanger is specially designed for the refrigerating sector and for
tasks where aggressive media are applicated.
- The welding of the plate cassettes takes place outside the gasket groove.
This practically eliminates the risk of corrosion attack in the gasket groove.
- When the welding takes place outside the gasket groove the disposable heat
transmission area is optimum utilized.
- The plate cassettes are supplied with a gasket construction increasing the ightness
concurrently with the increase of the working pressure.
- Like the traditional plate heat exchanger plates the plate cassettes fully comply with
the US 3A standard making this construction applicable for many sanitary tasks.
|
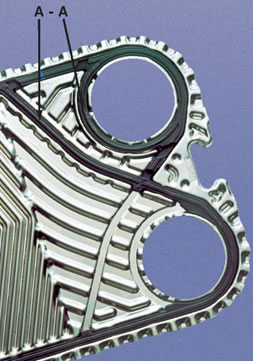
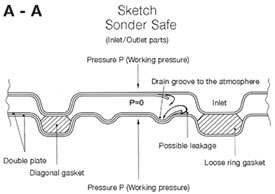
SONDER SAFE PLATES |
The Sonder Safe plates consists of two thin flow plates stamped together.
The two plates form a pair of plates which allows possible leaks to be seen from
outside between the two plates. This prevents a mixing of the products and warns
about internal leaks.
APPLICATION AREAS
- Milk and cream pasteurization.
- Sanitary water for food processing.
- Water for medical injection/ultra-pure water.
- The nuclear industry for safety reasons.
- District heating/tap water.
- Engine cooling.
|
|